Have you ever tried blasting? If you have ever blasted you will already be familiar with the following. If you have never blasted this is what you would have to look forward to once you don a blasting helmet.
Noise – the compressed air exiting the nozzle does so at supersonic speed. This generates an extremely loud noise that can be in excess of 120dba. This is much like an aircraft jet engine, except your face is only inches away from it.
Dust – as you blast the rust, removed coating and abrasive are pulverized into microscopic particles that creates a very thick dust cloud. It looks like a desert dust storm. In extreme cases it in impossible to see the blaster as he is enveloped by the dust storm. This dust is not safe to breath and will have long term health effects if inhaled over a period of time.
Heat – abrasive blasting is hot strenuous work. Much like holding onto a 3″ fire hose, it takes a lot of effort to tame the blast hose. In hot climates you will work up a sweat in mere minutes.
Poor visibility – with all the dust flying around, and the helmet window quickly frosting up, it soon becomes very difficult to see much past the end of your nose. Just to see the surface being blasted requires a lot of concentration and causes eye strain.
As if all those pleasures are not enough, you can also have to contend with being surrounded by millions of tiny aggressive abrasive particles, all flying around at 400 mph.
Unfortunately this is the “nature of the beast” of abrasive blasting and there is not much that can be done about the surroundings. But that does not mean we cannot do anything to protect the operator, and make it as comfortable and safe as possible, for them to work in this environment.
The following 8 Ways will help you keep your blaster’s safer and more comfortable.
8 Ways to Keep Blasters Safe & Comfortable
- Carbon Monoxide Alarms
- Clean Breathing Air
- Blasting Helmet
- Deadman Controls
- Protective Clothing & Ear Plugs
- Hose Safety Wires
- Abrasives & Silica Sand
- Safety Program
1. Carbon Monoxide Alarms
An invisible, odourless deadly killer. Carbon monoxide is a potentially deadly gas if it gets into the blasters breathing air supply.
There are 2 potential sources of this poisonous gas.
1. Compressor overheating. Oil lubricated compressors have the potential to generate carbon monoxide if the compressor over heats.
2. Contamination of the compressor inlet. If facing the wrong way against the wind, diesel driven compressors exhausts can get blown back into the air intakes. Parked vehicles, with their engines left running, emit exhaust that could be directed towards the compressor air intake.
There are 2 ways to deal with this life threatening gas.
1. Breathing Air Monitoring. A small sample of of the operators breathing air is taken from the breathing air filter and passed through a monitor. If the level of CO in the air is above a preset limit, usually 10ppm, an alarm is triggered. The alarm can be sirens or flashing lights.
2. Convert the CO to CO2. The human body can tolerate much higher levels of Carbon Dioxide than Carbon Monoxide. The allowable level of CO2 is 1,000ppm, compared to only 10ppm for CO.
All the breathing air is passed through a catalytic converter to convert any CO to CO2. This unit is also fitted with a CO monitor and alarm.


2. Clean Breathing Air
Blasters are totally dependent on the quality of air being supplied to their helmet. Not only does it need to be free of carbon monoxide, it should also be free of all impurities, particulate, oil and water, bad odours etc.
Most Government Safety Regulating bodies, i.e. OSHA, HSE, Work Cover etc have their own standards for air quality supplied to air fed respirators.
There are a variety of filters available for filtering the air prior to it entering the blasting helmet. In the industry of sand blasting the most common type is the large cylindrical filter illustrated below.
These contain several layers of filtering materials and absorbents to clean the air of particulate, oil mist, water vapour etc. The activated charcoal removes bad odours.
It should be noted this type of filter is only for freshening of the air. It cannot change the make up of the air, i.e. oxygen level, so the air needs to be fit for breathing before entering the filter.
These type of filters generally remove particles down to 0.5 microns in size. This is good enough in some countries. Other countries, i.e Australia, require a better level of cleaning than this, so additional filtering has to be added.
The most common trouble with this type of filter is the filtering element does not get changed often enough. The rule of thumb is the filter element should be replaced every 3 months or after 400 hours usage.
It should also be replaced immediately if any odour is detected coming into the helmet.
Stickers, as illustrated below, should be placed on the outside of the filter unit, not on the filter element, to record the date of the element replacement.
Note. The breathing air filter, hose and helmet are often permanently hooked up together. If there is no way of turning off the air supply to the filter, it will have air passing through it continuously, whether blasting or not. This needs to be taken into consideration when counting the hours of usage.
There is a noticeable difference in the taste of the air coming from an over used filter and a new filter cartridge.

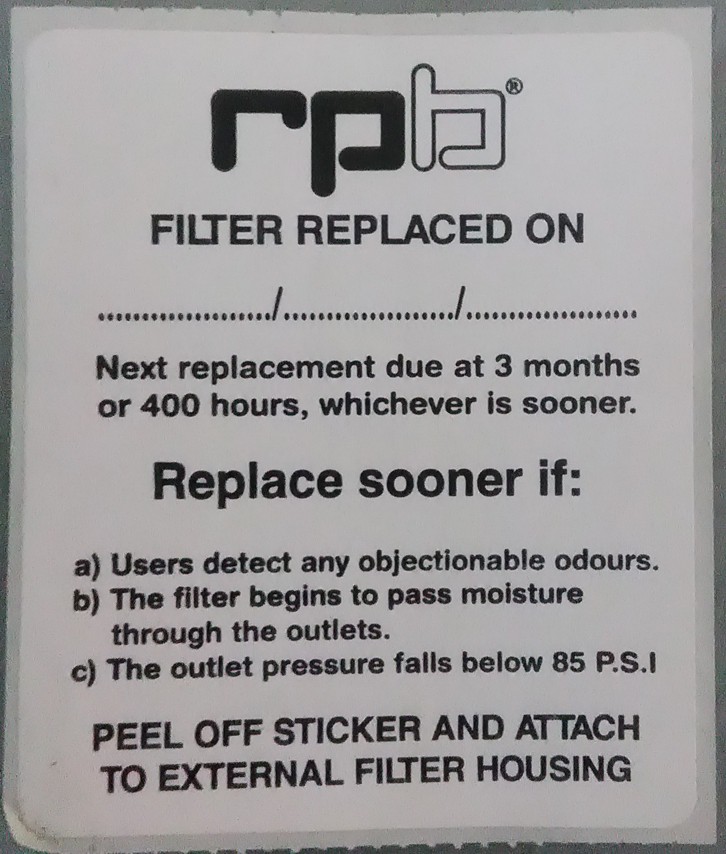
3. Blasting Helmet
A hand held welding mask with the tinted glass removed is not a blasting helmet. A cardboard box with a slot to see through, and a car wash sponge, stuck in the mouth to suck/filter air through, is not a blasting helmet. Both have been tried, and I’m sure there are even worse examples.
As with the breathing air supply most countries have rules and regulations governing the wearing of air fed respirators and helmets. And rightly so.
Blasters have to put up with noise as loud as a jet engine, millions of abrasive particles flying around at hundreds of miles/kilometers per hour, clouds of highly toxic dust, and their vision reduced to barely being able to see past the end of their nose. Not a nice place to be.
The one thing that can most improve their level of comfort is the blasting helmet. A good quality comfortable helmet can make a world of difference.
Obviously eyes need to be protected from the ricocheting abrasive particles. This is achieved by using a 1mm (1/32″) thick plastic protective lens.
With the constant bombardment of abrasive particles against it, the window will soon become frosted over and unusable. This is expensive to replace. Instead of constantly replacing this protective lens, a sacrificial lens is placed in front of it. This is a lot thinner and a lot cheaper to replace. These sacrificial lenses can be replaced one by one, or for faster production, a tear off system is available, similar to Formula 1 racing helmets.
Internals of helmets are generally either fully lined with foam padding, similar to a motorcycle helmet, or fitted with a head harness, similar to a hard hat. Foam lined helmets offer more comfort as they help to reduce noise levels inside the helmet.
During blasting huge amounts of potentially toxic dusts are generated. These dusts are created from the coating being removed and from the abrasive being used and breaking down. Old coatings often contain heavy metals that become breathable dust when pulverized by the blasting.
Combined with the breathing air filter, blasting helmets are essential in protecting blasters from breathing these dusts. A porous neck cuff allows air fed into the helmet to exit, without allowing dust or abrasive into the helmet.
Compressors generate heat as they compress air. How the air is treated after compression will determine the temperature of the air feeding the helmet. Air coolers and heaters are available to adjust the air temperature just before entering the helmet.
Air coolers are especially useful in hot climates. Simple and cheap, these devices can reduce unbearable breathing air temperatures down to comfortable levels.

4. Deadman Controls
Blasters should have their own deadman controls so they can independently stop and start blasting. If they rely on a pot tender to stop their blasting there is a potential for accident if the pot tender is not paying attention.
Deadman controls feature a handle that cannot be accidentally activated, it requires a deliberate 2 stage action by the blaster. This prevents blasting from accidentally being started if the handle is fallen onto.
Available in pneumatic or electric configurations. Electric deadman controls react instantly. Pneumatic controls take a longer time to activate, due to time taken for the air to travel through the twinline hose.
If the blast hose is 40 meters or more long, electric deadman controls should be used to avoid delays in valves turning on or off.

5. Protective Clothing & Ear Plugs
Protect blasters from flying abrasive particles with a blast suit, purposely made for the application.
Available with leather or nylon protection depending on abrasive being used.
Avoid headaches, ringing ears and permanent hearing damage.
Always wear ear plugs when blasting.
Cheap and simple.
6. Hose Safety Whip Checks
Compressed air stores and enormous amount of energy. When hoses burst, or couplings separate all that energy is suddenly released.
Unrestrained hoses, with heavy steel couplings on the end of them, can do a lot of damage. Fatalities have occurred.
Abrasive and sand blasting is one of the biggest consumers of compressed air. High pressures and high volumes require big hoses. The bigger the hoses are, the bigger and heavier the couplings on the end of hoses are.
Inevitably at some time hose couplings are going to disconnect unexpectedly. The risk of a heavy coupling hitting anyone in the vicinity can be greatly reduced with the use of steel wire hose safety cables, whip checks.
Each end is connected to either the adjoining hose or to a stationary piece of equipment.
In the event of a coupling opening or breaking the whip check will prevent the hose flying around uncontrolled.


7. Abrasives & Silica Sand
Although the process is still commonly referred to as sand blasting, sand is an abrasive that should never be used. River sand, beach sand and any sand containing more than 1% free silica are extremely dangerous to blasters and surrounding workers.
Crystalline silica is classified as a Class 1 carcinogen.
Sand has been banned for use as a blasting abrasive for many decades in most countries. When blasted sand will break down into a very fine dust. This dust is fine enough to remain suspended in the air. These airborne particles are so small they are easily inhaled. The tissue in the lungs reacts to these invaders and creates scar tissue around the dust particles.
This eventually develops into the deadly lung disease – silicosis. This disease can develop within weeks, or several years after exposure.
Whenever possible the item to be blasted should be done so using a recyclable abrasive. Most common is blasting steel products with steel abrasive.
Other recyclable abrasives are available to suit different blasting requirements i.e. glass beads, aluminium oxide, plastic media, etc. All these abrasives are recyclable and do not produce any harmful dust as they break down during use.
However, protective respirators and clothing, and adequate containment and ventilation must still be employed.
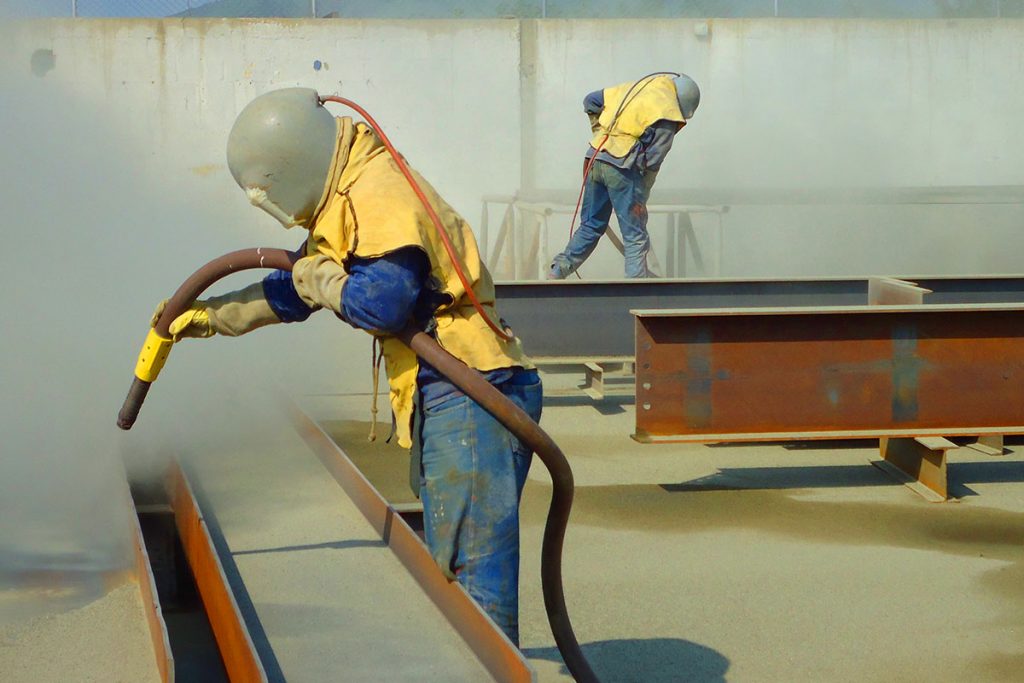
8. Safety Program
Aside for the previous risks specific to abrasive blasting, blasters are also subject to many other work place dangers and risks. Confined spaces, scaffolding, falling from heights, lead paint, explosion and fire, compressed air etc.
A workplace safety program, to train operators and prevent injury, should be developed.
A good program outline can be found here:
SSPC-Guide 17, Guide to Developing a Corporate Safety Program for Industrial Painting and Coating Contractors
http://shop.sspc.org/ST-000G17