We all know of the environmental damage, the waste and the general mess caused by open blasting. These are the reasons why it is getting harder and harder to do. Every year more rules, and more regulations.
So the trend in abrasive blasting is to try to reduce, as much as possible, the dust generated.
This 8 Ways will illustrate some of the ways you can do that on your blasting project. There is no perfect solution that is suitable for all applications. Sometimes a combination of one or more systems might be required to fully complete a project dust free.
With a lot of these systems you also get a bonus. Not only can you blast without creating environment damaging dust, you also get to use recyclable abrasive. And that can save you a fortune in abrasive, clean up and disposal costs. In most cases there will be some capital investment required in equipment. But that has to be offset against the money you can save blasting cleaner.
8 Ways to Create Less Dust on Your Next Blasting Project
- Use Steel Grit & Recycle
- Blastrac Dustless Blasters
- Blast & Vac
- Wet Blast
- Porta-Blast
- Containment
- Ventilation Fan
- Equipment Operation
1. Use Steel Grit & Recycle
This method of blasting is gaining more and more wide spread usage. As we know the most economical abrasive to use for blasting steel products is steel grit. Provided the grit can be captured and reused it is by far the cheapest way to blast. Abrasive consumption through breakdown is <0.5/kg per square meter. This is a fraction of the consumption rate of expendable abrasives.
The 2 critical factors for this to work are the ability to capture the abrasive and the ability to recycle the abrasive. If you are in luck the shape of item to be blasted lends itself to capturing the abrasive. Good examples are oil storage tanks and internal tanks of ships. Both of these are large steel structures that can be easily sealed to contain the abrasive. Not only will this produce less pollution, production rate increases due to the fast cutting speed of steel grit and the increase in visibility inside the chamber.
Easiest and fastest way to remove the abrasive after blasting is with high powered vacuum units. Alternatively the abrasive can be man handled or mechanically removed from the structure.
After recovering the abrasive it is passed through an abrasive recycling system. This is one of the most important parts of the machine. As the abrasive is being reused it needs to be cleaned to like new condition after every blast. The recycling system needs to thoroughly clean the good reusable abrasive of dust and over size waste.
A good example of adaption of this method are ship building facilities. The traditional way to blast ship sections is on the dockside using expendable abrasives. This is now being brought indoors into purpose built blastrooms using steel grit.

Less dust, less waste and no pollution.
2. Blastrac Dustless Blasters
If you have lots of flat areas you are in luck. If you are blasting beams, angles, small pipes, fittings etc, sorry this is not the machine for you.
The Blastrac Portable Enclosed Blaster uses the blasting power and productivity of a turbine wheel shot blaster. The turbine is fitted into a mobile walk behind Blastrac. The operator merely points the Blastrac in the direction he wants to blast, presses the start button and walks along behind it. The Blastrac is self propelling. Once the Blastrac has completed its blast the operator turns it around, to point in the opposite direction, and starts off blasting again.
As it is blasting, all abrasive and dust is contained and recycled within the enclosed head of the machine.
As the machine can continually recycle the abrasive, it enables steel shot to be used as the blasting medium. Steel shot can be recycled hundreds of times, and produces almost no dust. It is this continual recycling of the abrasive that results in such a small amount of waste being generated.
In fact the rule of thumb consumption rate for blasting steel products is 0.5kg/m2 or 0.22lb/ft2, (compared to 12-40kg/m2 for expendable abrasives). To put this into perspective that is 1/24th to 1/80th of the amount of abrasive and waste. During blasting 90% of the dust is created by the shattering abrasive particles as they hit the surface. Prevent this and there is virtually no dust.
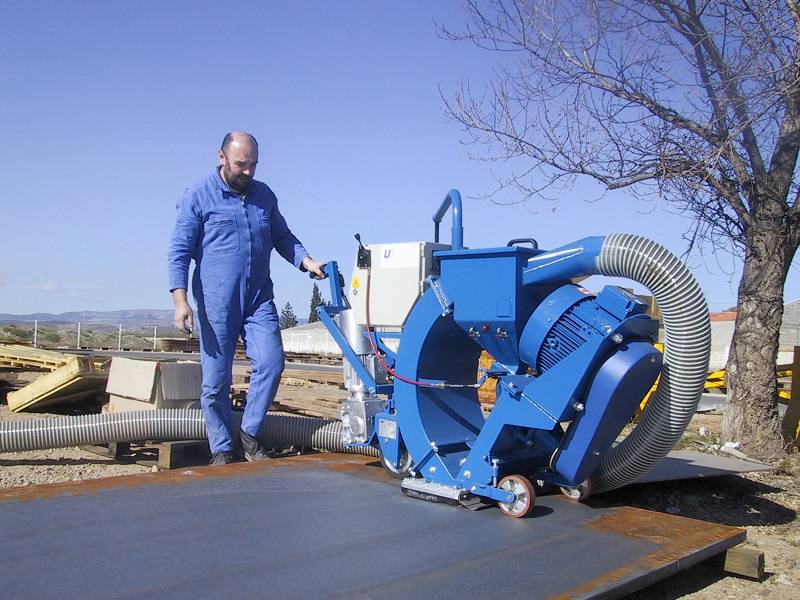
But that’s not the only advantage. Profits can be substantially increased with very high blasting production rates. One operator with a Blastrac can blast, in the same time, 6 to 8 times the area of a blaster with a nozzle. Instead of 10m2 (100ft2) per hour your operator is producing 60m2 (600ft2).
The high production rate is achieved due to the efficiency of the electric turbine throwing wheel. This method of propelling abrasive is at least 6 times more efficient, per kw or hp unit of power, than propelling abrasive with compressed air. When you throw 6 times the amount of abrasive, you blast 6 times as fast. So blasting 6 times faster equates to producing 6 times the income, in the same time period.
And at a fraction of the cost for abrasive and waste disposal. Furthermore there is no need to erect scaffolds, curtains and tarpaulins. No need to protect surrounding areas from dust and flying abrasives.
There are many applications that can use Blastrac equipment. The bigger and flatter the surface is, the more productive the equipment is.
In all instances the contractor will save time and expense to complete the project, and create no dust in doing so.
If you have large steel areas to blast, want to create no pollution, and want to earn more money doing it, this is the best way to blast.

3. Blast & Vac
Blast and Vac systems are very useful for touch up blasting or for blasting small areas. If the area you need to blast is big this might not be the best way to do it. Production rates are not very high and operator fatigue will play a factor. Weld seams, small area touch up work and spot blasting are ideal for this equipment. The area to be blasted also needs to be relatively flat, although there are corner attachments available.
The equipment consists of a blasting pot to generate the blast through a nozzle. The volume of the pot size is the main determining factor for how long you can blast without stopping to refill. The blasting nozzle is fitted into a cone shaped shroud (blasting head). The blasting head is held onto the surface of the part to be blasted. Rubber and brushes seal to the surface and prevent spillage of abrasive and dust during blasting.
Blast and Vac systems are design for use with recyclable abrasives. Most applications are for blasting steel products, therefore it does not make economical sense to use anything other than steel grit as the abrasive.
The equipment is fitted with either an air or electric driven vacuum pump. During use the vacuum is used to suck all abrasive and grit from the blasting head and transfer it via heavy duty suction hose to an abrasive re-cycler. This is one of the most important parts of the machine. Some systems use a very basic drum type re-cycler. This does not much more than collect the abrasive and dust, without any cleaning. Better systems use an adjustable reclaimer to thoroughly clean the abrasive. As the abrasive is being reused it needs to be cleaned to like new condition after every blast.
A well designed system will remove all dust and over size waste and ensure every blast is using clean correctly sized abrasive.
For as good as they are for preventing dust pollution, the main draw back with Blast & Vac systems is their low production rate (generally <5m2/hr) and difficulty to use. The blasting head is heavy and it does not take long for operators to become fatigued.
All blasting is conducted inside the blasting head so the operator cannot see the actual blast. It is case of blasting any area and seeing the result after the head is moved. Often this can mean having to re-blast missed areas.
4. Porta-Blast
If the item to be blasted is relatively small it might be able to be transported to a blasting facility. But for bigger items, or remote work sites, this is not feasible. So instead of bringing the work piece to the blasting facility, bring the blasting facility to the workpiece.
Porta-Blast is a plug and play, all in one temporary blast and paint enclosure. Instead of creating a huge mess, or transporting your parts around, a temporary blasting and painting facility can be set up wherever you need it.
The facility is made up of the following components:
- Temporary weather proof enclosed work place
- Blasting dust ventilation
- Paint overspray filtration
- Abrasive blasting and recycling
As the blasting is conducted within the enclosure, all the abrasive can be captured and recycled. This allows virtually any type of abrasive to be used. Steel grit, garnet, aluminium oxide, glass beads, plastic media, ceramic beads etc. All can be blasted without dust pollution and recycled, and the amount of waste generated is reduced to the bare minimum. All these different abrasive types allow a huge variety of work to be performed in a Porta-Blast temporary blastroom, right there on site.
More details of this system can be found here:
5. Wet Blast
A variety of wet blasting systems are available and all suppress dust to a greater or lesser degree.
The simplest system is an attachment that is fitted to the outside of the blast nozzle. This is connected to a hose pipe. As the air and abrasive leave the nozzle a shroud of water surrounds it. Dust suppression efficiency estimated at 80%.
Next up is a water injector. This device is fitted between the nozzle and nozzle holder. Within the fitting a series of small holes permit water to be injected into the air stream just prior to it existing the nozzle. As this system is injecting water into the air, it requires a hydraulic pump with sufficient pressure to raise the pressure of the water above the pressure of the compressed air. It cannot be used with just a hose pipe. Dust suppression efficiency estimated at 90%.
Top of the food chain are systems that have the blast pot filled with water and abrasive to create a slurry. This slurry is then blasted through the hose and nozzle. As the air stream is fully saturated with water this method is virtually free of all dust. These are also the most expensive systems.
Consideration has to be made for the coating that will be applied after blasting. As the blasted part is wet, it will flash rust quicker than a dry blasted part. Some coatings are flash rust tolerant, some are not. Rust inhibitors may also be used with wet blast, but it needs to be checked it is compatible with the subsequent coating.
Although eliminating dust, all the above systems create an abrasive and contaminant waste slurry that must be contained and not allowed to pollute the environment. There is no point in eliminating one pollutant but creating another.
6. Containment
Sometimes the part to blast is just too big to be blasted in any other way except by open blasting. The huge size and shape of the part, and the area to blast, render every other option un-viable. Think of a bridge, ship or water tower. It is not every day they are uprooted and transported to a blasting facility. They are also far to big to be processed in a Porta-Blast facility.
So open blast it is. Now the objective is to eliminate dust generation as much as possible. And this is done with containment. If you are lucky the part can be tightly encapsulated and all the abrasive captured. If this is the case you can likely use steel grit and recycle it. Refer to earlier section for the benefits of this. Some parts cannot be wrapped enough to fully contain the abrasive so they are blasted with expendable abrasives.
Generally a scaffold structure is erected around and on the part. Containment sheeting is fixed onto the scaffolding. Sheeting specific for the purpose is fitted with eyelets and fastened to the scaffold with rubber or bungee straps. If the part is to be painted after blasting, flame retardant sheeting should be used.
A correctly designed and assembled containment system can eliminate virtually all blasting dust pollution.

7. Ventilation Fan
Here is a cheap and simple method to capture and reduce dust from any enclosed structure. These ventilation fans are available in a variety of air volumes, and with air driven fans for painting applications.
Use with the dust sock to capture most of the dust instead of just blowing it from one place to another. Once the sock is blocked it can be emptied and washed a few times.
Be aware you need space. The sock is 6 meters long when blown up.

8. Equipment Operation
This might seem pretty obvious but it is surprising how many times it can go wrong. When any equipment is new it runs perfectly and all is ok. But we all know after a few weeks in the field things change. A blasting site is not the friendliest environment for man and machine. And the actual operators are sometimes not fully aware of how the equipment should work.
So as the intention is to reduce dust levels, it is important to keep your equipment running correctly and in tip top condition.
Here are 3 things that often go wrong but can be easily fixed. All lead to generating more dust than necessary.
1. Blasting pressure at the nozzle. Unless you check it you will never know what it is. Could be 80psi. Could be 100psi. The blaster can probably feel the difference, but do they feedback? Unlikely.
If the air pressure at the nozzle drops, the abrasive velocity decreases. And slower abrasive particles cut slower. And when they cut slower you need to throw more abrasive to do the job. More abrasive means more dust, more cost and more waste.
Best way to check is with a hypodermic needle gauge. This is a pressure gauge fitted with hypodermic needle that is inserted into the blast hose, just behind the nozzle. This is the true blasting pressure reading, not what the gauge reads on the blast pot. If it’s low, you need to get it up. Every 1psi pressure loss equates to 1.5% production loss.
Probable causes:
- nozzles worn out ’till oversize and the air compressor cannot keep up with the additional demand
- restriction in fittings or piping on blast pot leading to restricted air flow
- air hose or blast hose too small for the distance
2. Dust collector malfunction. Usually this is the filters becoming blocked. The dust collector stills sucks, but maybe at only 50% capacity. As the dust collector slowly blocks over time, no one notices. Unfortunately you will end up with a more dusty environment
.
Probable causes:
- filters have reached the end of their useful life and require replacing
- reverse pulse cleaning system malfunction, pneumatic or electric (refer to 8 Ways To Keep Your Dust Collector Running Smoothly for trouble shooting tips)
- moisture in compressed air. This is a killer for filter cartridges. The pulsing air must be dry. If it is even slightly damp the filter material will soak up the moisture and dust will not release from the filters.
3. Insufficient abrasive cleaning. When using using recyclable abrasives the abrasive should be thoroughly cleaned after each blast, ready for reuse. Uncleaned abrasive can lead to system blockages, contamination of the blasted surface and excessive dust. Most recycling systems use some kind of airwash to clean the abrasive after every pass. If this malfunctions the above issues will occur.
Probable causes:
- dust collector malfunction. The ventilation dust collector is often used to provide the airflow for the airwash system. If the dust collector is not sucking correctly the airwash does not work.
- separator incorrectly adjusted and allows dust to remain with good abrasive
- air intake is blocked preventing airflow through the separator
So the moral of the story is keep your equipment maintained and in good operating order and you will create less dust and save money.
